Gloveless or Less Gloves? Regulatory Trends and Automated Solutions
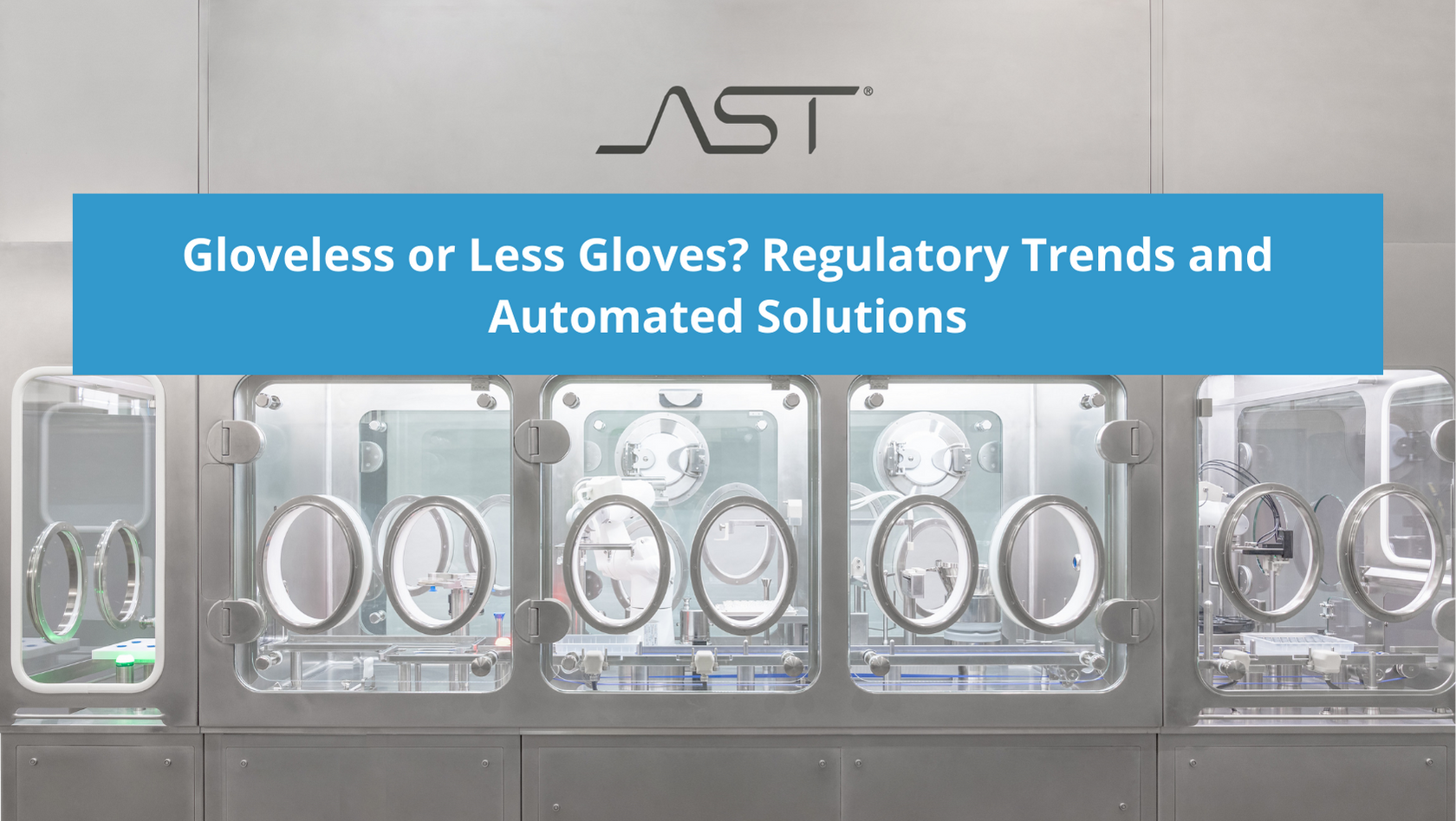
The following article is part 2 of a blog series that has been adapted from AST’s VP of Sales and Marketing Josh Russell’s recent article in Cleanroom Technology. In part 1, we discussed considerations for isolator configurations and AST’s approach to integrating automation in our new barrier technology solution.
The most important questions to consider in any fill-finish setting include how you will handle planned and unplanned interventions. Automating in such a way that you can optimize the most sensitive of routine operations and anticipate the best interventional solutions to maintain operational uptime is paramount. This is one essential area where the practical application of a gloveless isolator runs into limitations, but the overall push toward automation has been a clear net positive. It’s one thing to say you have a gloveless solution—it’s another thing entirely for robotic tools to have demonstrated competence in the full breadth of possible interventions needed in an operational context. A gloveless isolator is only as good as the quality and scope of the automation it offers, and even the best automation has a risk of failure, however small. And if any sort of failure is possible, then the actual choice isn’t between “glove and gloveless” but between a glove port and a door. The question then becomes in what sterile setting is it appropriate to open a door? The answer is never. In a manufacturing context, sacrificing a batch in the name of gloveless convenience is simply not an option.
Regulatory Trends Towards Automated Solutions
It’s been said the perfect intervention is the one you don’t have to perform. This attitude is the impetus behind our industry’s push to reach more stringent quality standards and is always the goal of an aseptic processing operation. A point of emphasis in the new Annex 1 is utilizing better barrier systems and advancements like robotics and automation where feasible to improve overall sterility assurance and reduce instances of human intervention. Much like the regulatory push towards the use of isolators, as technological advancements provide a path towards new possibilities in product quality and reliability, regulatory standards will be reevaluated. As automation is a clear prerequisite to effective isolator arrangement, Annex 1’s highlighting of robotics, automation, and rapid solutions should be noted. As technologies like telemanipulation continue to improve in the application of routine and non-routine interventions, it stands to reason that regulatory emphasis on automation will continue.
A Clear Path Forward: Automation Strengthened by Gloved Redundancies
How then should we proceed if our goal is to offer fill-finish professionals the best, most effective solutions that are regulatorily robust?
What operators are looking for, and what regulations like Annex 1 are speaking to, is a focused quality-by-design approach that leverages solutions, automated or otherwise, to design out risk and design in quality. This means innovating for the sake of effectiveness and not getting lost in the realm of ideas. We don’t want our automated solutions becoming the proverbial knife slicing the soda can in half—that’s the wrong type of cutting-edge. The goal should be advancements that can be implemented seamlessly into an improved containment control strategy while prioritizing the safety and viability of whatever sterile parenteral product is being produced. This approach includes the use of precisely engineered robotics and automation, simplified designs that minimize the likelihood of mechanical failures, and using appropriate troubleshooting tools and failsafes for unplanned interventions. In this respect, there are a myriad of situations where a well-placed, well-designed glove port is a key to strengthening automated solutions and sterility practices rather than a hindrance.
That’s why at AST, our mission is to provide robotic and automated aseptic processing solutions designed and optimized to meet the real-world operational realities of fill-finish manufacturing while envisioning a future where greater sterility and product quality are possible.
A recent example of this commitment is the AST Glove Tester, a turnkey solution designed in concert with the AST isolator. A fully integrated glove testing system with data and batch reports accessible through ASTView, this is a complete solution with a docking cart, chargers, and a self-verification system for four testers. The system also interlocks with start-of-batch operations to maintain sterility protocols.
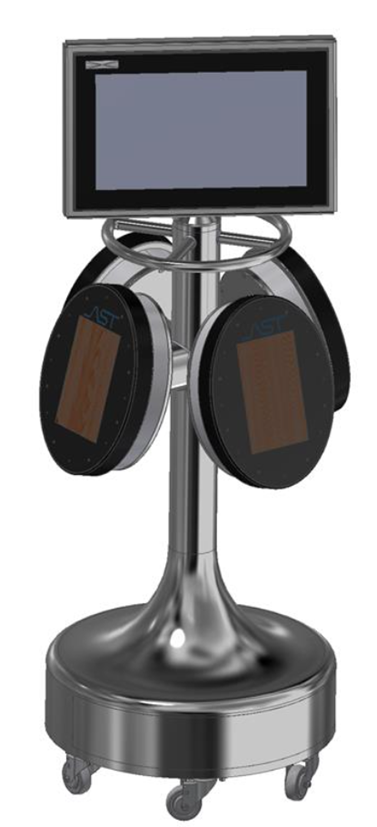
Figure 1 – The AST comes with 4k high-definition touchscreen display and a docking cart with four testers.
As pharmaceutical manufacturing pushes towards innovative ways to strengthen aseptic processing, and as advancements continue to unveil new possibilities, the considerations laid out here on the most effective ways to integrate automation and isolator technology are ones that fill-finish professionals industry-wide must continue to revisit.
Learn how AST can provide your organization with the next generation of high-quality isolator technology – contact our experts today.