American-Made, Worldwide Benefit: Raising the Bar in Isolated Fill-Finish Manufacturing
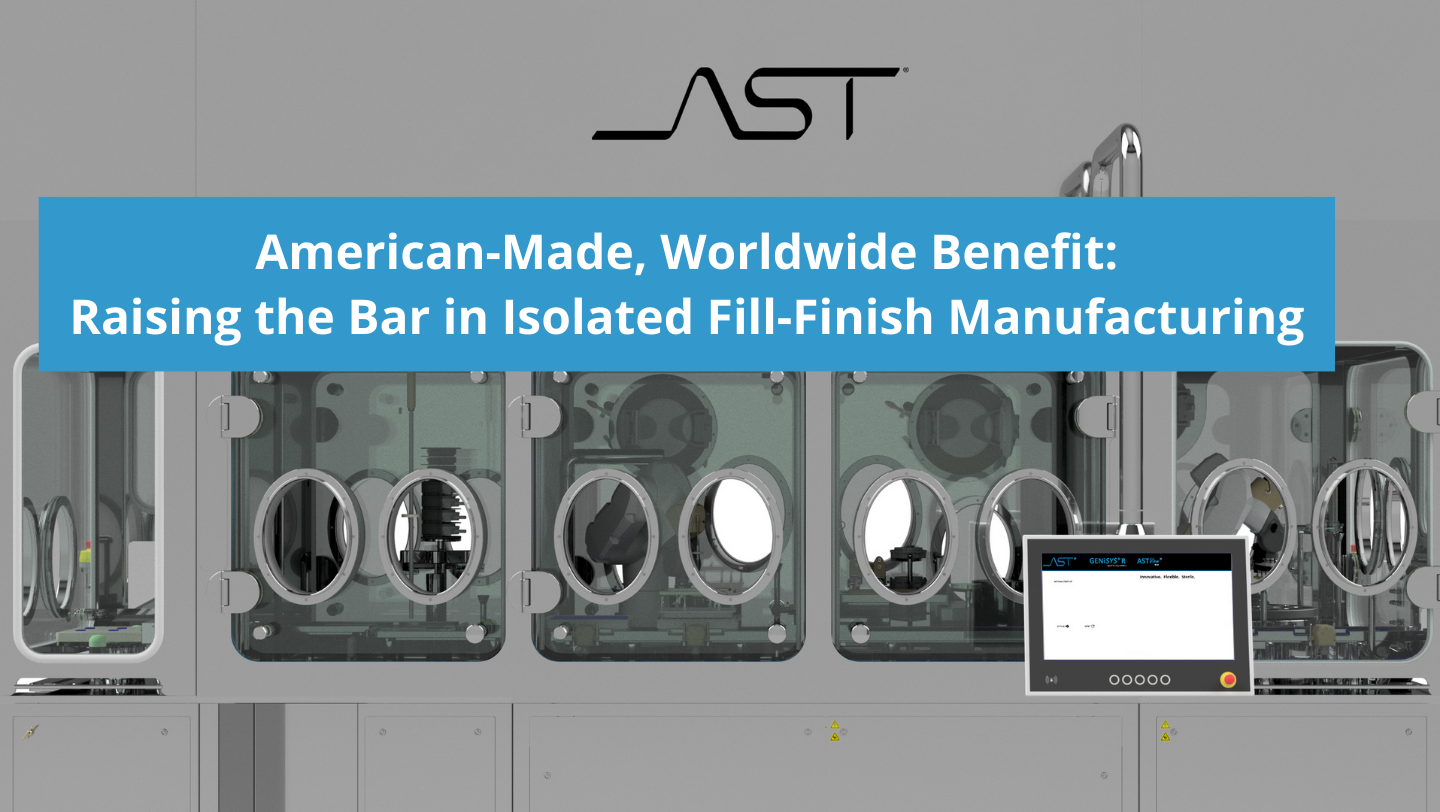
When AST produced its first fill-finish solution in 2006, two key convictions drove that early innovation: A commitment to imagining a never-before-seen aseptic multi-format processing system that was versatile and flexible, and a desire to produce robust, American-made aseptic fill-finish products.
Ahead of the release of our new isolator, we wanted to explore our commitment to domestic production and how it empowers our customer-focused approach. The principle behind a truly American-made product goes beyond a slogan. It’s a statement about the level of quality, intention and ingenuity executed in every aseptic solution we provide. As our CEO & President recently wrote, a clear vision of end-to-end domestic production has been one of the driving creative forces behind AST from the onset.
The new isolator—designed and manufactured in collaboration with the tremendous team at Germfree and featuring CURIS System’s groundbreaking rapid vapor Pulse™ Technology —is the next articulation of that founding conviction. Designing a state-of-the-art fill-finish isolator directly informed by feedback from customers and engineered with the same innovative approach that gave life to our first pioneering ASEPTiCell was an opportunity the entire AST team was eager to undertake. The result is an advanced product that reflects the rigorous design standards our customers have come to expect.
These exciting benefits will be accessible to customers worldwide as this new isolator technology is a bottom-line difference-maker across the market. For AST, American-made doesn’t only mean employing American ingenuity on behalf of our domestic customers but leveraging that same ingenuity, and the power of a localized supply chain, to meet the needs of all our industry partners abroad. By addressing common pain points in isolator manufacturing and servicing, our goal is to provide a solution designed to meet and anticipate the evolving demands of the liquid pharmaceutical market as a whole.
A Customer-Focused Aseptic Processing Solution
So where does the proverbial rubber meet the road? How exactly does this approach percolate down to aseptic fill-finish professionals?
An AST procured, designed, and serviced isolator offers:
A Quality Difference – It may seem obvious, but when you’re in the business of engineering next-generation technological solutions, you strive for the best: solutions that are well-crafted, well-constructed and cutting-edge. One of our core principles at AST is a dedication to continuous improvement, and our Isolator solution is a steel-and-glass expression of this ongoing process. The decision to bring the design of the isolator in-house meant that we could bring the same high standard of attention to detail that we bring to our filling and closing systems to every aspect of isolator design. From construction to setup to functionality, AST and Germfree Engineers have worked together to fine-tune our isolator to meet our customers where they’re at and remedy some of the most prominent obstacles in isolated fill-finish processing.
A Service Difference – Launching any aseptic fill-finish operation is a complicated, exact process and having a complete solution, with both the barrier technology and fill-finish system fully integrated and possessing the same design philosophy, has a variety of benefits. A single, unifying Human Machine Interface for both the fill-finish system and the isolator will provide unparalleled integration and efficiency that will be supported by a localized supply chain, ensuring ultimate efficiency in machine implementation and support. As always, service issues will be coordinated and fulfilled completely by our responsive Customer Care services. We understand just how important ramp-up and upkeep services are, and an AST-designed isolator will make those services all the more efficient in launching and maintaining our systems for our customers.
An Industry Difference – Manufacturing supply chain practices have been under the microscope since the COVID-19 pandemic. Pharmaceutical production, in particular, has been hit with a barrage of challenges over the past five years and has seen current supply chain assumptions challenged as shipping interruptions and material shortages, amongst other factors that have come to the forefront. Recent analysis has called for the pharmaceutical manufacturing industry to adapt and account for a certain level of volatility. A streamlined, responsive, and localized supply chain is a practical way to prepare for the unknown and build resilience into supply chain strategies.
And when you couple this with industry-defining lead times on isolator manufacturing and decontamination technology that executes a full cycle in 60 minutes? That’s a recipe for a new standard in aseptic processing.
This isolator cements AST as a single-source, turnkey provider for aseptic processing solutions. From the outer hinges on the shell door all the way down to the precise IPC technology used to measure some of the most valuable, targeted parenteral drug products on the market, customers will have an intuitive, meticulously engineered isolated fill-finish system. Learn how AST can provide your organization with the next generation of high-quality isolator technology – contact our experts today.