4 Ways the GENiSYS® R Sets the Standard in Aseptic Manufacturing Flexibility
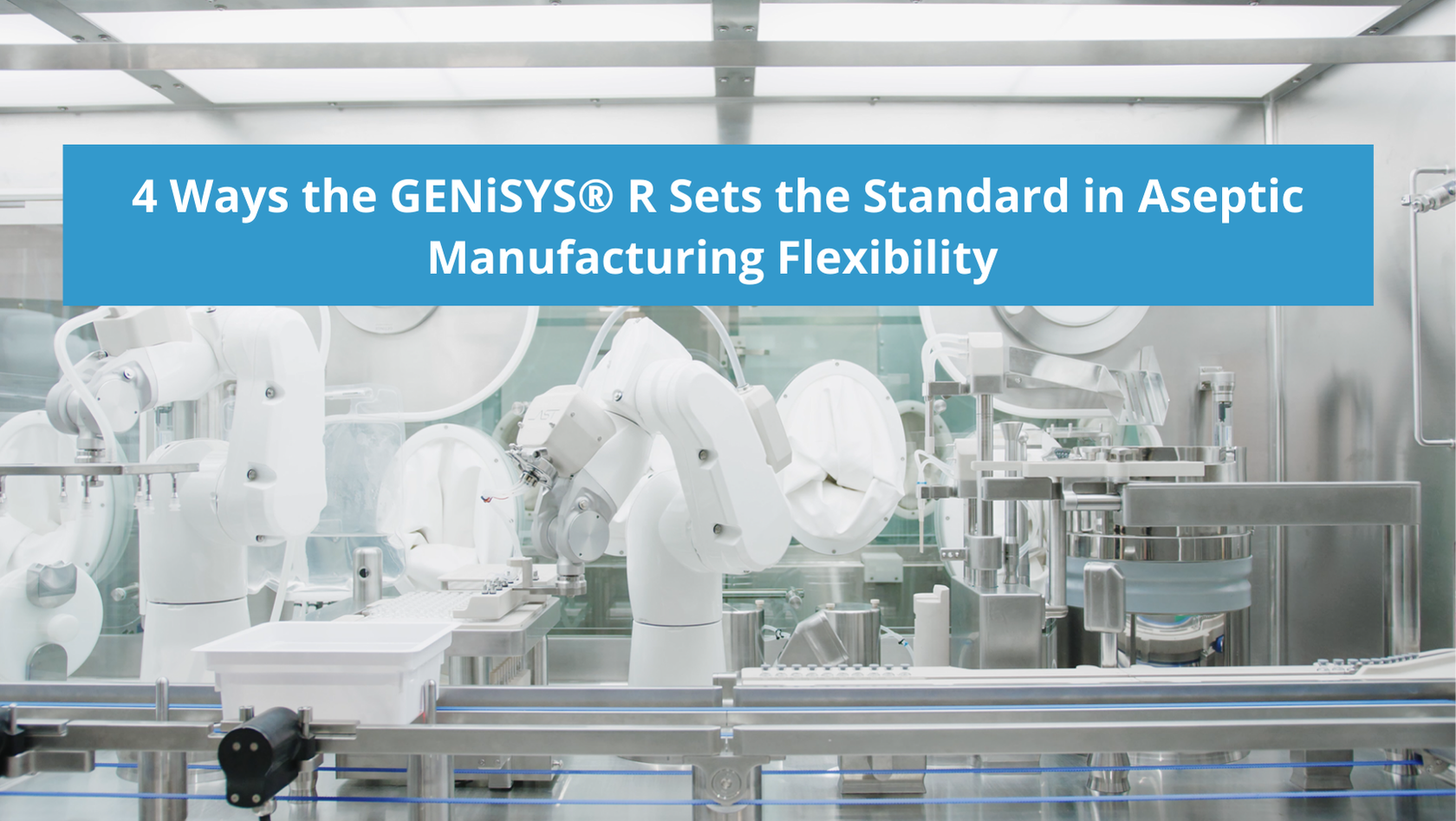
Pharmaceutical manufacturing continues to see growth in the field of highly targeted, high-value liquid pharmaceuticals. Increasingly, entities like CDMOs, are looking at the most effective ways to implement adaptable, streamlined multi-modal operations designed for uptime and time-to-market optimization. In the initial phases of planning your aseptic fill-finish operation, there are many decisions to make both contingent on where you are at in the drug development lifecycle and the demands of the particular type of product being produced. Does a manual or automated process make sense? What is the facility footprint of the operation? How does a potential aseptic fill-finish system fit within an operation’s containment control strategy?
With an ever-changing market, manufacturers are looking to achieve optimal flexibility and high utilization from their aseptic processing systems. From a compliance and production standpoint, automation and robotics have become the clear industry preference for sensitive parenteral drug products. At AST, our approach to innovation and service is rooted in a focus on providing solutions that meet the most challenging product and regulatory requirements faced by many aseptic processing professionals. The GENiSYS R represents the latest in AST’s commitment to innovative, flexible aseptic processing. This aseptic filling line offers modular, semi-automated and fully automated solutions designed to meet the demands at every stage of development, from clinical to commercial.
Here are four ways the GENiSYS® R promotes superior flexibility and adaptability across the life of an operation:
Modularity
One of the design advantages of AST machinery is the use of modules throughout the filling and closing lines. Lead time and operational changeover are crucial to the time-to-market equation for pharmaceutical manufacturers, many producing drugs that address critical patient needs. The built-in philosophy at AST approaches fill-line configurations in an adaptable way, able to meet the customer’s specifications. Like grabbing the right tools for the job from a toolbox, our modular approach enables AST engineers to capture 90% of requirements with our existing solutions, which allows very rapid configuration and delivery. This approach minimizes or altogether eliminates technical risks with a selection of tested and standardized “building blocks” applicable for the majority of fill-finish product requirements.
The available modules on the GENiSYS R are:
- SABO – Semi-Automatic Bag Opening
- ABO – Automatic Bag Opening
- MTO – Manual Tub Opening
- ATO – Automatic Tub Opening
- FCM – Fill / Close Module
- LPM – Lyophilization Prep / De-Nesting Module
- VSM – Vial Sealing Module (also available in a linear configuration)
Muli-format/multiple product capability
Having the ability to process a full range of vials, syringes, and cartridges on the same line is crucial to implementing a flexible manufacturing approach. A selection of RTU containers that can be filled and closed with minimal changeover time gets at the heart of many of the issues faced by today’s drug manufacturers. A static fill-finish operation dedicated to the output of single product is no longer effective in many supply chain configurations. The GENiSYS R can process the most well-known and utilized containers in the industry as well as specialty tray packs and tubs.
Fewer change parts
With an efficient approach, automated operations open up new possibilities for change parts and changeover times. This is a conviction that AST carries throughout all of our aseptic processing systems—If there’s a way to simplify a design and eliminate a change part, our engineers will find it. Depending on the configuration of the GENiSYS R, entire modules are designed to operate without change parts (the ABO and ATO). Finding a fill-finish partner that not only employs this approach but is committed to finding innovative ways to effectively reduce the number of change parts going forward will add and enhance operational efficiencies.
A unified engineering approach
When time is of the essence, having a solution that scales seamlessly can play a vital role in the success of the operation. Utilizing completely different technology at the various stages of development costs valuable time both in the tech transfer and revalidation processes. Additionally, the training required for each new piece of equipment or user interface is a substantial investment of time and other resources. Our goal at AST is to have a consistent, precise engineering philosophy that is present in every solution we implement. When you use the same tools, the same IPC (In-process weight check) technology, the same Human Machine Interface, etc., scaling up becomes efficient and smooth, eliminating the need for re-training, revalidation, and long machine changeover times. Additionally, complete process traceability across systems allows for successful tech transfers.
The GENiSYS R is a fully integrated turn-key solution. Check out the full demonstration below and contact our experts today: