The AST team recently returned from New York City, the site of Interphex 2024, and to say we came back motivated would be an understatement. The show was teeming with enthusiasm as life sciences professionals from across the globe gathered in the Big Apple for the premier pharmaceutical and biotechnology event. The stage was set for three full days of innovative showcases, thought leadership, and industry connections, and from the moment the doors opened on day one, the checkered flag dropped, and the Javitz Center became an inflection point for non-stop conversations and exchanges on the biggest breakthroughs and best ideas in the pharmaceutical industry.
For AST, this marked the most concentrated and largest showcase at Interphex to date, as we introduced a full lineup of fill-finish innovations that our team has been hard at work developing, refining, and implementing. The featured solutions not only represented standalone improvements to our most fundamental technologies but, in a flagship moment for the company, we introduced the AST isolator that integrates exclusively with our aseptic fill-finish lines for a first-of-its-kind complete, integrated AST solution.
The exhibit that AST brought to Interphex 2024 is a comprehensive, forward-looking aseptic processing product and service advancement and represents the only 100 percent American-made turnkey fill-finish solution available on the market. Our goal in bringing this forward was to meet the demand of a rapidly evolving marketplace filled with new pharmaceutical products and maturing regulatory standards complicated by volatile supply chain realities. This is a complete solution, featuring a new class of isolator technology, designed in collaboration with Germfree, and an aseptic processing system that utilizes robotics and automation for fill-finish production within a traceable, cGMP manufacturing environment. This solution is applicable for a full range of products, from modern, targeted, small-batch therapies to traditional large-scale pharmaceutical production. Major highlights include:
- A streamlined, responsive, and localized supply chain for complete fill-finish servicing and 24/7/365 support
- Drastic reduction in equipment delivery lead time and service request time
- One-touch automation, with barrier technology and the isolator running on a single, centralized HMI, with comprehensive integrated batch recording
- State-of-the-art automated environmental monitoring interventions and data recording
- New, innovative fill-finish decontamination system with expanded material compatibility and a compete decontamination cycle times within an hour, including aeration
- Precise, unified engineering design for seamless scaling throughout the drug development process
With this offering, AST will have a complete, integrated solution in place for our customers that guarantees sterility and compliance, and remains flexible enough to scale an operation to meet diverse customer requirements, all while optimizing for real-time manufacturing realities and scaling considerations (technology transfer, changeover times, validation times, material compatibility, etc.)
A closer look at AST’s latest innovations
The Automated Environmental Monitoring Solution from AST is an innovative tool to augment EM process interventions and enhance batch recording. The EM plate-changing tool utilizes pre-sterilized, serialized settling plates that come preloaded in a cassette dispenser which is aseptically introduced into the fill line. Each plate has a serial number that is logged and tracked in the integrated HMI batch records, allowing for precise correlation of each plate with a specific batch. Plate changes are automated through the HMI, saving process time on typically ergonomically unfriendly gloved interventions. The assembly comes double-bagged and is introduced via RTP. This is a quality-by-design solution that remedies key pain points in fill-finish processing. Highlights include:
- RFID tracking of cassette and plate tracking via serial number
- Automated plate data recording
- Operator-less plate installs and removal
- Eliminates routine intervention and potential causes of contamination.
- Eliminates risk of creating a false positive
- More operational uptime
- Consistent with Annex 1’s emphasis on automated solutions
- Fully Integrated with fill-finish system’s HMI
AST’s new Haptic Telemanipulation leverages Force Dimension technology working in conjunction with Staubli robotics. This was a collaborative conceptional demonstration in an aseptic processing context. With potential application across the entire fill-finish line, haptic force telemanipulation eliminates certain high-risk non-routine interventions, as well as ergonomically unfriendly and/or time-consuming routine interventions. The operator will utilize a 6-axis haptic device with sensorless force feedback. Anti-collision is digitally programmed. AST’s booth demonstration featured a use case demonstration of telemanipulation in the Vial Sealing Module of the GENiSYS® C: operator-controlled pick and place interventions. This innovation represents the most advanced, practical application of telemanipulation in a fill-finish setting and first to utilize Force Dimension haptic technology.
Technical highlights include:
- High Degree of Freedom (DoF)
- Demonstrated use for routine interventions
- Demonstrated use for non-routine interventions
- Aseptic technique and conditions maintained throughout
AST’s GENiSYS® C
The exhibit also featured the latest updates to the GENiSYS® C, an advanced and intuitive solution for the automated aseptic processing of high-value, targeted liquid pharmaceutical products. Well-suited for small-scale filling applications, including research and development, engineering runs, clinical trials, through to commercial production runs, the GENiSYS® C offers operational capacity to process nested, custom and ready-to-use vials, syringes, and cartridges. The isolated design specifically offers the ideal automated and environmental setting for patient-centered medicinal products. Other value points include:
- Flexible, modular design to meet evolving product and pipeline demands of today’s fill-finish market
- Enhanced with nest transfer automation to reduce human intervention
Notes from the Road: AST Takes Center Stage…Literally
It’s fair to say that attendees were as excited as we were about the lineup of cutting-edge technology AST had on display, as we had the chance to connect with hundreds of conference participants throughout the event. In truly Interphex fashion, people were eager to see live demonstrations of features like the automated EM solution and haptic telemanipulation, the latter of which attendees had the chance to experience themselves in a user-controlled demo that tested the eye for precision with a pin place-and-push challenge. (The author regrets to inform you that, according to multiple reports, he himself did not pass the challenge).
The enthusiasm was solidified on Day One when Interphex selected AST’s exhibit for the coveted Best in Show Award. Interphex’s Exhibitor Awards were established to recognize leading conference participants for knowledge, innovation and state-of-the-art technologies. The “Best in Show” category specifically “recognizes levels of quality, production goals, and objectives—ultimately transforming critical and affordable life-enhancing ideas to finished drug products.”
CEO and President Joe Hoff said of the award, “This is a tremendous honor… Preparing for Interphex this year was a significant undertaking, so to win the award now is especially meaningful. I’m particularly proud of our team. This is our first award recognition from Interphex, and it couldn’t have come at a better moment to recognize the hard work put in by every individual across every department at AST. This truly was a team effort and years in the making.”
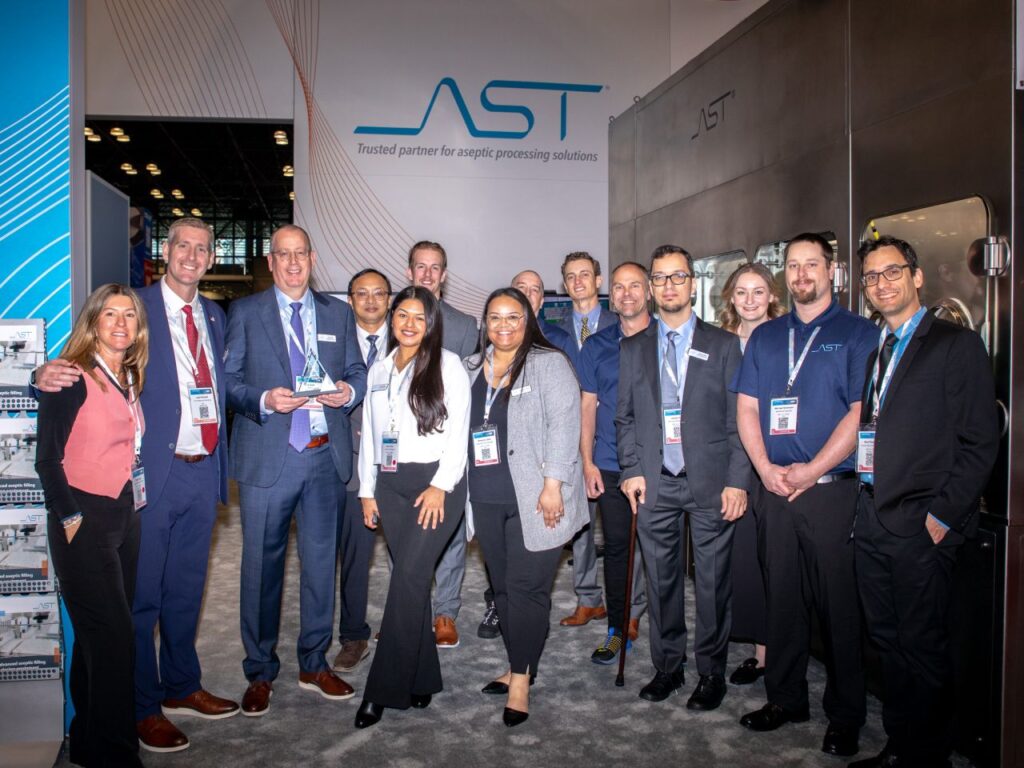
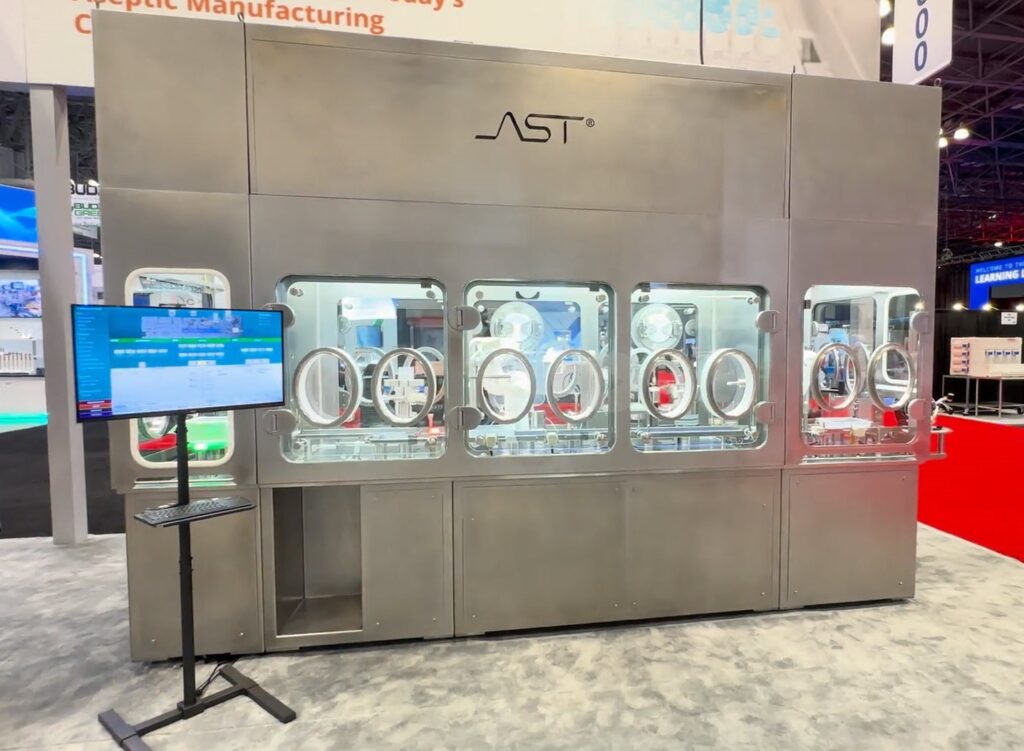
The momentum of the event didn’t stop there. AST was asked to participate in the thought leadership segment of the conference, The INTERPHEX Learning lab, a new format vetted and designed in partnership with the American Association of Pharmaceutical Scientists (AAPS). The education-centered format featured presentations selected by a 3rd party scientific committee and focused on expert-led discussions on the most pertinent topics relating to the biotech and pharmaceutical industries. AST Vice President of Sales and Marketing Josh Russell was featured on day one, presenting a session titled Fill-Finish Innovations: Environmental Monitoring & In-Process Checks. Josh covered the practical and strategic merit of utilizing automation in a fill-finish setting and went into depth on recent advancements in environmental monitoring and IPC methods.
On Wednesday, Steven Ng, AST CTO and VP of Customer Service, was joined by partner CURIS System and participated in a moderated panel discussion: Reimagining Decontamination: Low-concentration Hydrogen Peroxide Protocols. Joined by other industry leaders, this was a data-based discussion on the latest research on decontamination processes and the results and downstream effects of utilizing low-concentration (7%) rapid HP vapor protocols in isolated aseptic operations. This was an opportunity to do a deep dive on this new innovative technology, examine some common assumptions about the conventional use of hydrogen peroxide, and explore the ramifications of what a safer, faster decon method could mean for fill-finish professionals.
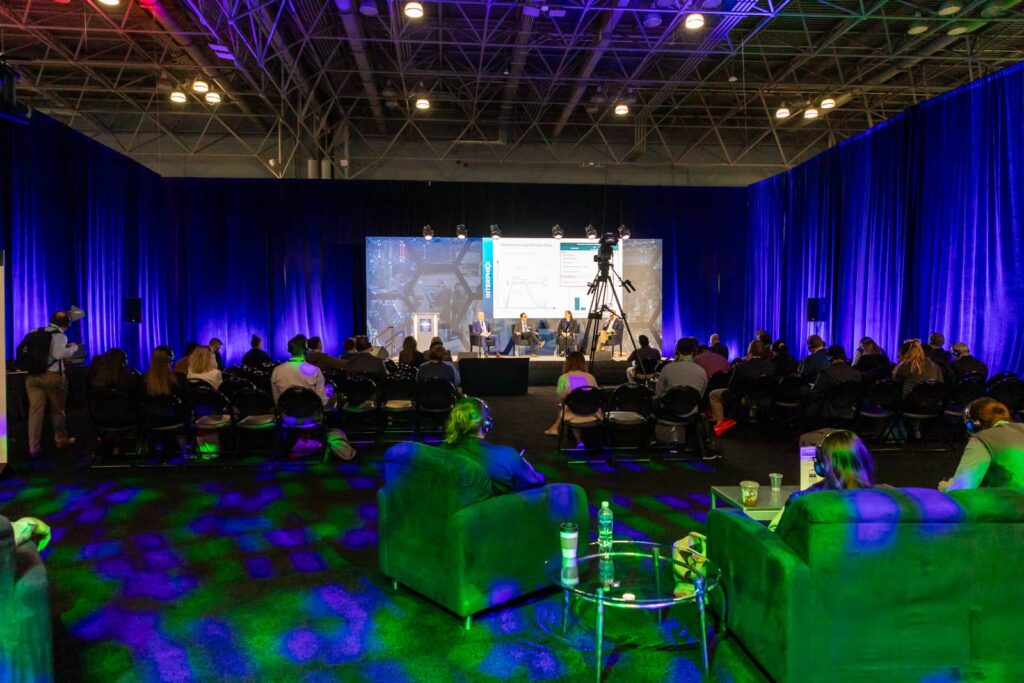
Interphex 2024 was, as in years past, an excellent opportunity to connect with like-minded people across the industry, people who value the life sciences and are passionate about innovations that get us closer to the goals we collectively hold: breakthroughs in the efficacy, productivity, and accessibility of life-improving and life-saving modalities. That’s why AST was thrilled to demonstrate the next stage of our commitment to enhancing the efficiency, productivity, and safety of flexible aseptic manufacturing processes.